ION the comparison was just a bit of a lark, a poke at the Keppe mob.

Tinman I'm not measuring the input or efficiency with that, I'm using them to sense current. I am aware of how to measure the power
and it requires smoothing of the DC. But there is no electrical output now, this is to generate using a generator coil.

Give me time.
It will be an acceleration under load motor, when I get that happening I'll measure the power.
Any real comparison should be with another pulse motor because the point to it is the charging coil is used to help turn the rotor.
I had the charging coil there to begin with just to raise the voltage of the capacitor C2 to dump through the motor coil. But I decided
I might as well use it to help turn the rotor as well. as just an inductor it had not much loss because it has only 1.2 Ohms resistance.
And when I use it to help the rotor the raised voltage it produced only dropped from 26 volts to 23 volts in C2.
I''ve now found a suitable way to return all of the inductive energy for the charging coil to reuse so there is only one battery.
I'm not claiming anything except a new and novel pulse motor principal. It's a resonant charging circuit for a pulse motor and the
charging inductor is used to help drive the rotor as a second phase, and it now returns all the inductive energy from the motor coil to a capacitor
and back through the charging coil. It's not built as best as the idea could be done it's a prototype. The last couple of changes I made have made it much better.
It spins the rotor more efficiently now and with more torque than it did in the video's, so it's improved. A better design would be used for a motor for a
practical purpose one with more coils and more magnets for better efficiency and torque.
I'm not after the "spike" with this, except to enhance current through the coils to drive the rotor.
This is the single battery setup a few people want, so as to do away with the charge battery for experiments.

As far as I am aware no one else is using these principals in just this way for pulse motors.
I can't believe no one gets it.

Kidding.
I guess I should make a simpler drawing for the inductive energy return on a regular pulse motor circuit though.
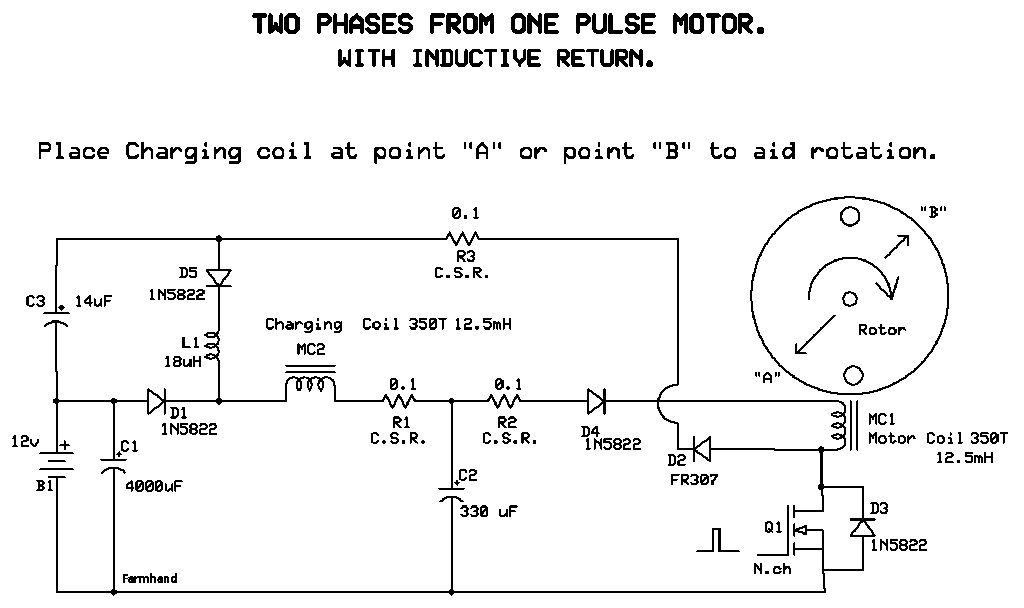
Two Phases from One Pulse Motor ?
Here is a circuit with just the inductive energy return to a capacitor for the motor coil to reuse, without it having to go to the battery.
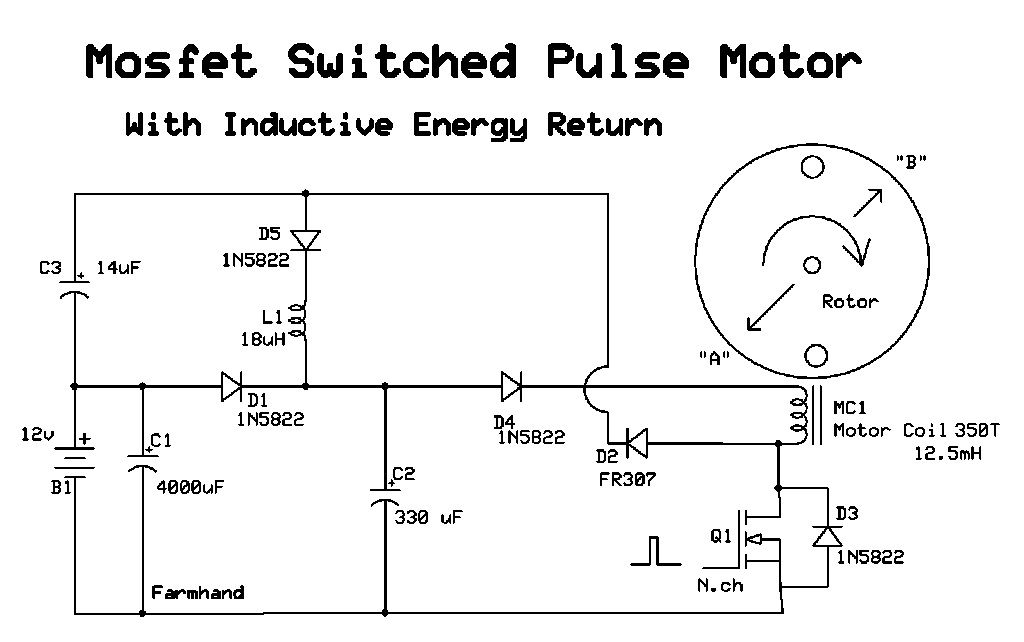
Two Phases from One Pulse Motor ?
I can provide scope shots of the energy being returned and reused, if anyone is interested.
Cheers